Know Your Fiber: Viscose Rayon (aka Bamboo, Viscose)
Posted on August 01 2018
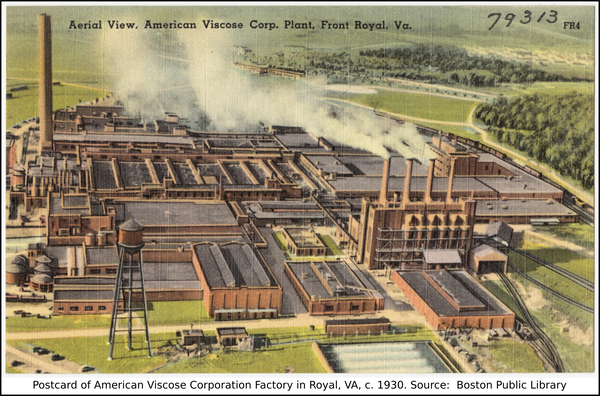
In the late 19th century, the first semi-synthetic fiber in history was invented – viscose rayon! Known as artificial silk until its rebranding as rayon in 1924, rayon has become a significant part of our fiber landscape.
In the yarn and fiber world, we most frequently run into rayon when it is labeled as bamboo or viscose. More recently, you can also buy viscose rayon labeled as rose fiber (having been sourced from the cellulose of rose bushes), or even purchase viscose rayon fiber that comes from seaweed. While these fibers are often advertised as eco-friendly because they come from plants, that is not necessarily the case. As you will see as you read on about the history of viscose rayon manufacture, this lovely, silky fiber has not always been kind to the workers manufacture it, and has had a history of adverse health effects on the workers involved in its manufacture right up to the present day.
In 1838, the French chemist Anselme Payen extracted the first pure cellulose from plant matter, and patented the first rayon fiber in 1855. Cellulose fascinated scientists throughout the Western world. Many experimented with it, including Joseph Swan, a well-known inventor who developed the electric light bulb in the U.K. around the same time that Edison invented the light bulb in the U.S. Joseph Swan experimented with using this refined cellulose as a filament for light bulbs. Although better materials were ultimately found for this purpose, cellulose fiber also captured the imagination of his wife, Frances, who produced crocheted articles with this new fiber for an exhibition in 1885.
However, the development of a process to produce a durable cellulose fiber in commercial quantities had already been undergoing continued and significant development in France before the Joseph and Frances Swan. Count Hilaire de Chardonnet, popularly known as the Father of the Rayon industry, patented his technique of creating artificial silk (the name at the time for what we know now as rayon) in 1884, and exhibited it in 1889 at the Paris Exhibition. By 1891 his first artificial silk factories were built to produce this new wonder fiber, branded as Chardonnet Silk. Cheaper than silk, but with a feel very close to silk, this new fiber was a wonder of science and art. Some adjustments to the formula were made over the next few years (the first artificial silk was extraordinarily flammable, but this was fixed with a little chemistry trick using ammonium sulfide). Soon, clothing made with artificial silk began to be more common, and demand for this new fiber was high. U.K. chemists Charles F. Cross and his partner Clayton Beadle worked to further develop artificial silk production, and by 1905, the first viscose rayon plant opened in the U.K. Only a few years later, in 1910, the first artificial silk plant was established in the U.S.
A short and somewhat abbreviated version of viscose rayon production goes something like this. All rayon begins with pure cellulose. This cellulose is treated with a caustic soda, and goes through a number of curing processes and chemical treatments, including a process called Xanthanation in which it is mixed with carbon disulfide. The resulting material is dried and ground into a powder, and is dissolved in yet another caustic solution to form the viscose, the viscous solution from which viscose rayon receives its name. Allowed to stand for a period of time, the viscose solution is strained and then extruded through spinnerets, which land in a bath of sulfuric acid, forming rayon fiber. The fiber is then washed to remove any residual chemicals and make it safe for the wearer.
By the time rayon fiber and fabric hits the market, there are no traces of any chemicals that could harm the person wearing it. The same can’t necessarily be said for the factory workers, either in the past or today. The workers in the artificial silk factories of the late 1800s and early 1900s were working on the cutting edge of fiber technology for the time. Increased understanding of chemistry allowed for the introduction of artificial silk to the world, but unfortunately it came with a price for the people who were in the factories that created this miracle fiber. While there are rather stringent chemical safety laws in many countries today intended to protect factory workers and give them legal recourse should businesses not keep their employees safe, these laws were largely non-existent at the time the first rayon was being manufactured in the West. And, it is worth noting, laws designed to protect factory workers both in the U.S. and internationally are not always applied even today. Of the many potentially harmful chemicals that were (and still are) used in producing viscose rayon, it turns out that it is carbon disulfide (a chemical used in one of the early curing processes) that is the most dangerous of all.
The dangers of carbon disulfide on human health was not unknown. As early as 1851, Anselme Payen noted that it could be dangerous to workers. Only few years later, the first known medical report on the damage caused by carbon disulfide was released in France by Dr. Guillaume Duchenne de Boulogne, soon followed by another report a few years after that to the French Academy of Medicine. Used in the rubber industry before it was ever used in the artificial silk industry, factory workers in the mid-1800s were all too frequently experiencing symptoms ranging from terrible dreams and various physical symptoms to outright insanity.
Workers for the new artificial silk industry of the late 1800s-early 1900s began to experience the very same symptoms from exposure to carbon disulfide that the rubber workers did just a generation before. Presented with these new patients, doctors were able to declare with very little ambiguity that carbon disulfide was to blame. Physicians in Europe and the U.S. strongly recommended that better ventilating techniques be used, and further recommended that workers be rotated between jobs to avoid excessive exposure. These recommendations would be followed with varying degrees of efficiency and efficacy over the next several decades.
Throughout the rest of the 1900s, all the way through the end of the century, there would be occasional reports in the U.S. and in Europe of carbon disulfide poisoning among rayon mill workers, and even among residents living near rayon factories. Factory strikes would sometimes try to address the dangers of working with carbon disulfide in poorly ventilated factory environs, which varying degrees of success throughout the 20th century. The U.S. Occupational Health and Safety Administration standards for safe amounts carbon disulfide exposure were set in place to try and protect workers (as well as its European equivalents), but the U.S. agency received criticism from workers’ organizations that those standards were not stringent enough – a complaint that has continued up to the present even as rayon manufacture has moved away from the U.S.
Concerned about the impact of rayon manufacture on workers’ health, scientists began to look for ways to create rayon without carbon disulfide. In the 1970, Lyocell rayon began to be developed, with the process continuing to be improved through the early 1980s. Unlike viscose rayon, Lyocell rayon production does not use carbon disulfide at all. On top of that, there is very little waste product at the end of the process. The safer factory environment and more environmentally-friendly rayon was much lauded, and continues to be used to this day. However, Lyocell is more expensive to make. Because of this, the much less expensive viscose rayon is still the predominant type of rayon on the market.
By the late part of the 1900s, viscose rayon manufacture began to migrate from factories in U.S. and Europe to factories in various parts of Asia where it could be made for much less money. As the manufacture of this fiber became cheaper than ever before, its presence in the world marketplace multiplied. Unfortunately, the same questions of worker safety from carbon disulfide in rayon factories are still present toady, even if they aren’t reported as widely as they were when substantial viscose rayon production was happening in the U.S. and Europe. Worker protections organizations have been focusing on Chinese and Indian factories quite a bit over the last decade. Although most countries have set legal exposure limits for worker exposure to carbon disulfide, these are not always enforced. In one incident in India, a factory was documented as having carbon disulfide levels 12 times higher than the legal limit. A few years later, a Chinese study in 2012 found that 10% of rayon workers they examined showed symptoms associated with excessive carbon disulfide exposure. And these are just a couple examples of many.
On top of the human health impact, it is increasingly looking like rayon production in Asia is also damaging old-growth rainforests in that part of the world. Although bamboo is a renewable resource from which to get cellulose, is has unfortunately become increasingly common for cellulose suppliers and rayon manufacturers to not be entirely honest about where their cellulose comes from. By labeling their viscose rayon as bamboo when it is not, rayon manufacturers are essentially attempting to greenwash their product. Bamboo is cheap, but is turns out that cutting down trees in the rainforests is even cheaper. As awareness of this practice has increased, so has regulation. The U.S. Federal Trade Commission has been cracking down on rayon fiber and fabrics labeled as bamboo entering the U.S. over the past several years. In order for viscose rayon fiber to be labeled as bamboo in the U.S., it is required that the cellulose must come entirely from bamboo.
So, where does this leave us as crafters and fiber lovers? Here at Northwest Yarns, we have a deep sense of discomfort when it comes to using fiber from industries that harm the health of their workers. Additionally, we really don’t want to have a hand (however inadvertently) in the destruction of the amazing, but quickly diminishing, old-growth forests of Asia. And yet, rayon is hard to avoid. Some of the yarns we have sold have been blended with viscose rayon, and we currently sell bamboo viscose fiber to spin as well. It is a lovely, lustrous fiber with similar qualities to silk, but quite simply more affordable and therefore more accessible to the many crafters out there who are cost conscious. One thing we have done is ensure from our bamboo viscose fiber supplier that the spinning fiber we are currently advertising as bamboo genuinely is. In regard to the health risks to factory workers, we have queried some of our suppliers about safety of the factories from which they get their bamboo viscose/rayon, but even they aren’t necessarily 100% certain if their own suppliers are protecting their workers’ health. That said, every single one so far has expressed concern and awareness about this issue.
Retail shops such as ours are the last point in a long supply chain, and while we are not the only ones asking questions about issues such as these, we will continue to do so until we are satisfied with the answers. Can viscose rayon be made without further destroying old-growth forests? Yes. Bamboo is a completely viable alternative to cutting down old-growth forests and it is a relatively quickly renewable resource. Can viscose rayon be made without damaging the health of factory workers? Yes. But is requires that companies purchase, install and maintain factory equipment that can recapture the chemicals used and produced during the manufacturing process. We don’t have to destroy old-growth forests to get rayon, and we shouldn’t be willing to accept that it is inevitable that a certain percentage of factory workers will experience health issues from manufacturing rayon. What we need to do is be aware, and work together to hold rayon manufacturers responsible for engaging in safe and ethical practices now, and in the future.
Follow US